CODEM’s Revolutionary Approach to Sustainable Manufacturing in CALLUM SKYE Project Results in Unprecedented CO2 Savings.
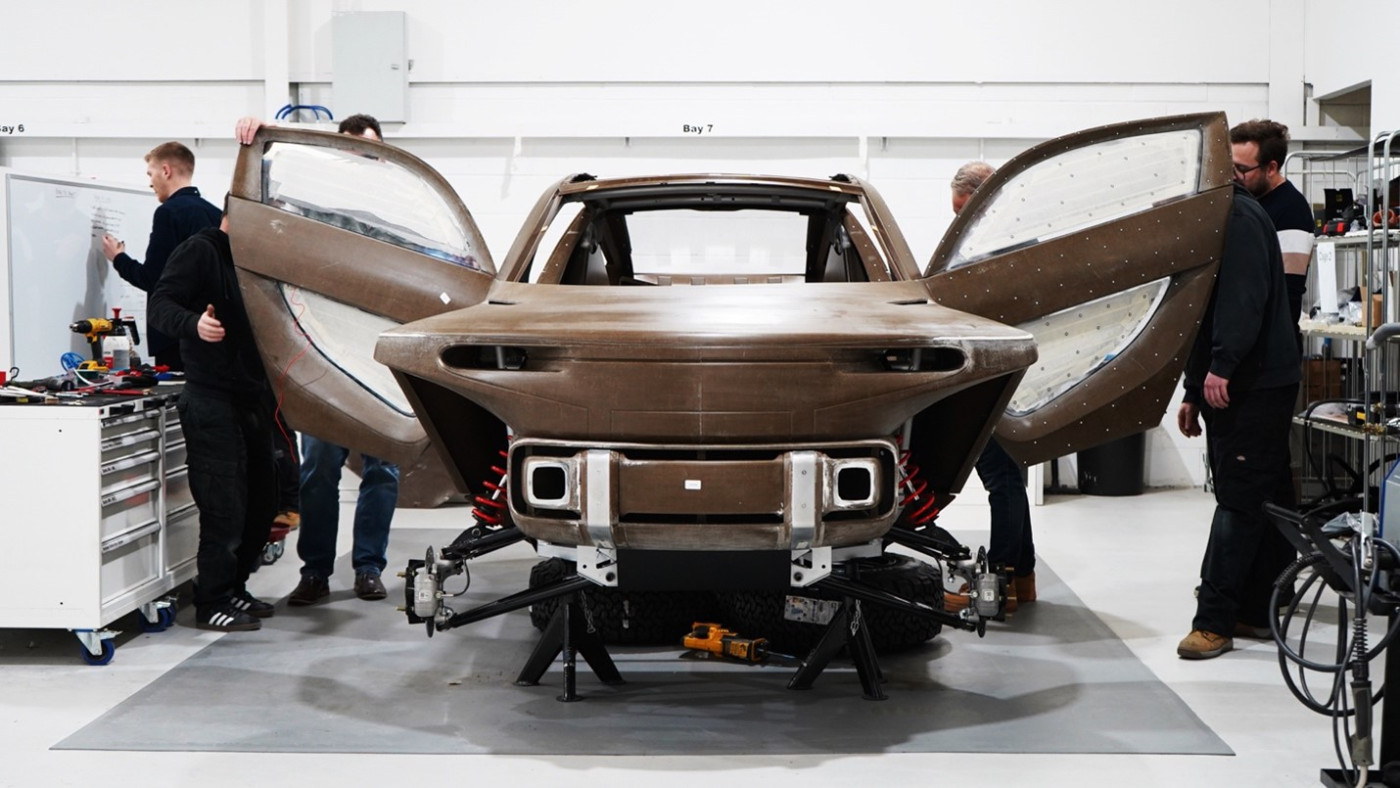
The ground-breaking CALLUM SKYE project demonstrates performance engineering, boasting a 35kWh, ultra-fast charging battery, sportscar performance, and lightweight body panels and structure. Through the project, CODEM demonstrated their commitment to innovation, sustainability, and excellence in advanced composite solutions.
CODEM partnered on the project, producing cost-effective, sustainable body tooling and panels for the SKYE, ensuring high-quality components for the initial low-volume production, whilst minimising material usage, cost and energy consumption.
The emission savings achieved through the project as a result of CODEM’s approach to sustainable manufacturing were impressive and groundbreaking.
Using a direct tooling to part approach for the initial low-volume production, CODEM designed and manufactured tools for each body section, reducing material usage, cost, and energy consumption.
CODEM’s approach includes the following innovative strategies, underpinning the focus on improved sustainability and reduced embodied CO2 emissions:
Sustainable Tooling Materials: All direct tools were made using Ru-bix Tooling Boards’ 100% bio-content HALO-S, providing an ideal balance of cost, performance, and sustainability.
Flax Fibre Bodywork: CODEM replaced traditional carbon fibres with flax fibre, grown and harvested in Scotland. This reduces transport, CO² emissions, and supports the UK economy, with flax plants absorbing CO² during their growth.
Bio-Based Resins: Traditional epoxy resins were replaced with bio-based resins. The selected resin, SHD Composite Materials’ MTB350, contains 30% bio-content and has an excellent shelf life at room temperature, eliminating the need for cold storage and supporting wider CODEM’s sustainability goals through reduced energy usage.
CODEM’s innovative approach in the SKYE project achieved substantial CO²e savings of over 10,000kg on the build of the prototype vehicle alone, setting a new standard for sustainable manufacturing. This success showcases CODEM’s ability to deliver high-quality, sustainable solutions that provide both environmental and economic benefits.
The CALLUM SKYE project highlights CODEM’s commitment to sustainable manufacturing and innovation. By integrating advanced composite solutions and eco-friendly materials, CODEM not only meets high-performance standards but also significantly reduces environmental impact. This case study serves as a testament to CODEM’s leadership in delivering revolutionary, sustainable manufacturing solutions.
To achieve Net Zero emissions, industry's operations must be overhauled by implementing locally sourced, sustainable supply chains. Supply chain emissions are typically 5.5 times higher than a company's direct emissions, with downstream fossil fuel use for transport and energy remaining the primary source of global CO²e output. As part of their sustainability efforts, CODEM sources 95% of our inventory from UK-based supply chains. Furthermore, 100% of the materials and consumables for the SKYE project come from UK-only supply chains, supporting the UK economy, and reducing CO²e emissions.
The CALLUM Skye project was supported as part of the Niche Vehicle Network (NVN) 2023 Production Readiness competition, funded by the Department for Business and Trade, via the Advanced Propulsion Centre, and delivered by the Niche Vehicle Network.